Flange Facing Machine: Essential Tool for Precision Pipe Flange Preparation
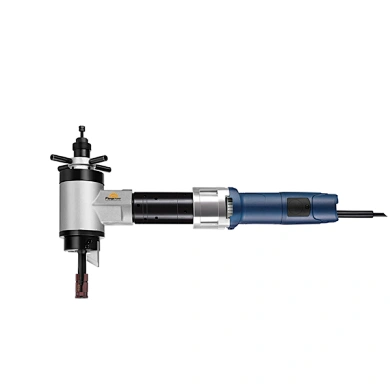
# Flange Facing Machine: Essential Tool for Precision Pipe Flange Preparation
## What is a Flange Facing Machine?
A flange facing machine is a specialized tool designed for machining and refinishing the sealing surfaces of pipe flanges. These machines play a critical role in pipeline maintenance, repair, and installation by ensuring proper flange face flatness and surface finish – essential factors for creating leak-proof connections in piping systems.
## Key Applications of Flange Facing Machines
Flange facing equipment finds extensive use in various industrial sectors:
– Oil and gas pipelines
– Petrochemical plants
– Power generation facilities
– Water treatment systems
– Shipbuilding and marine applications
These machines are particularly valuable when working with large diameter flanges or in situations where removing the flange for machining would be impractical or cost-prohibitive.
## Types of Flange Facing Machines
### Portable Flange Facers
Portable units offer the advantage of being brought to the job site, eliminating the need to remove flanges from their installed position. These compact machines typically feature:
– Lightweight designs for easy transport
– Adjustable mounting systems for various flange sizes
– Electric or pneumatic power options
### Stationary Flange Facing Machines
Larger stationary models provide increased stability and precision for shop-based operations. These machines often include:
– Heavy-duty construction for industrial use
– Advanced control systems for precision machining
– Capability to handle very large diameter flanges
## Essential Features to Consider
When selecting a flange facing machine, several key features should be evaluated:
– Cutting capacity (minimum and maximum flange diameters)
– Power source requirements (electric, hydraulic, or pneumatic)
– Material compatibility (ability to machine various metals)
– Surface finish capabilities
– Portability and setup requirements
– Tooling options and availability
## Benefits of Using Flange Facing Machines
Proper flange preparation with dedicated facing equipment offers numerous advantages:
Keyword: Flange facing machine
– Improved sealing performance by creating optimal surface finishes
– Reduced downtime by enabling in-situ repairs
– Cost savings compared to flange replacement
– Increased safety through proper gasket seating
– Compliance with industry standards for flange surface preparation
## Maintenance and Operation Tips
To ensure optimal performance and longevity of your flange facing machine:
– Regularly inspect and replace cutting tools as needed
– Keep machine components clean and properly lubricated
– Follow manufacturer guidelines for setup and operation
– Store the machine properly when not in use
– Periodically check alignment and calibration
## Industry Standards and Specifications
Flange facing operations must comply with relevant industry standards such as:
– ASME B16.5 for pipe flanges and flanged fittings
– API standards for oil and gas applications
– ANSI specifications for surface finish requirements
Proper flange preparation using a dedicated facing machine helps ensure compliance with these critical standards.
## Choosing the Right Machine for Your Needs
Selecting the appropriate flange facing equipment depends on several factors:
– Frequency of use (occasional vs. regular operations)
– Range of flange sizes to be serviced
– Available power sources at job sites
– Budget considerations
– Required precision levels
Consulting with equipment specialists can help identify the most suitable machine for your specific application requirements.