Tape Manufacturing Process and Techniques
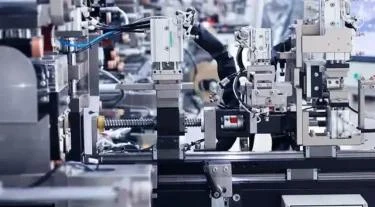
# Tape Manufacturing Process and Techniques
## Introduction to Tape Manufacturing
Tape manufacturing is a complex process that involves multiple stages to produce various types of adhesive tapes used in numerous industries. From packaging to electrical insulation, tapes serve essential functions in our daily lives.
## Raw Materials Used in Tape Production
The primary components of most tapes include:
– Backing material (plastic films, paper, cloth, or foil)
– Adhesive (rubber-based, acrylic, or silicone)
– Release liner (for some tape types)
– Additives (for UV resistance, flame retardancy, etc.)
## The Tape Manufacturing Process
### 1. Backing Material Preparation
The process begins with preparing the backing material. For plastic tapes, this involves:
– Extruding polymer resins into thin films
– Stretching the film to achieve desired thickness and strength
– Treating the surface for better adhesive bonding
### 2. Adhesive Application
There are several methods for applying adhesive:
#### a. Solution Coating
The adhesive is dissolved in a solvent and then coated onto the backing material. The solvent is evaporated in drying ovens.
#### b. Hot Melt Coating
The adhesive is heated until molten and then applied directly to the backing material.
#### c. Water-Based Coating
Similar to solution coating but uses water as the carrier instead of solvents.
### 3. Drying and Curing
After adhesive application, the tape goes through drying ovens to:
– Remove solvents or water
– Cure the adhesive for optimal performance
– Achieve proper tack and peel strength
### 4. Slitting and Rewinding
The large rolls of coated material are then:
– Cut into narrower widths using precision slitters
– Rewound onto smaller cores for packaging
– Inspected for quality control
## Specialized Tape Manufacturing Techniques
### 1. Double-Sided Tape Production
This involves:
– Coating adhesive on both sides of a carrier material
– Applying a release liner to protect one side
– Precise tension control during manufacturing
### 2. Foam Tape Manufacturing
Special considerations include:
– Laminating adhesive to foam substrates
– Maintaining foam integrity during processing
– Controlling thickness consistency
### 3. Electrical Tape Production
Key features:
– Specialized rubber-based adhesives
– Flame-retardant materials
– High dielectric strength requirements
## Quality Control in Tape Manufacturing
Manufacturers implement rigorous quality checks:
– Adhesion testing (peel strength, tack)
– Thickness measurements
– Tensile strength evaluation
– Visual inspection for defects
– Environmental resistance testing
## Environmental Considerations
Modern tape manufacturing focuses on:
– Reducing solvent use
– Implementing water-based adhesives
– Recycling production waste
– Developing biodegradable tape options
## Future Trends in Tape Manufacturing
Emerging technologies include:
– Nanotechnology-enhanced adhesives
– Smart tapes with sensing capabilities
– Improved sustainable materials
– Automated production systems with AI quality control
The tape manufacturing industry continues to evolve, meeting the growing demands of various sectors while addressing environmental concerns and technological advancements.
Keyword: tape manufacturing